Nordhavnstunnel
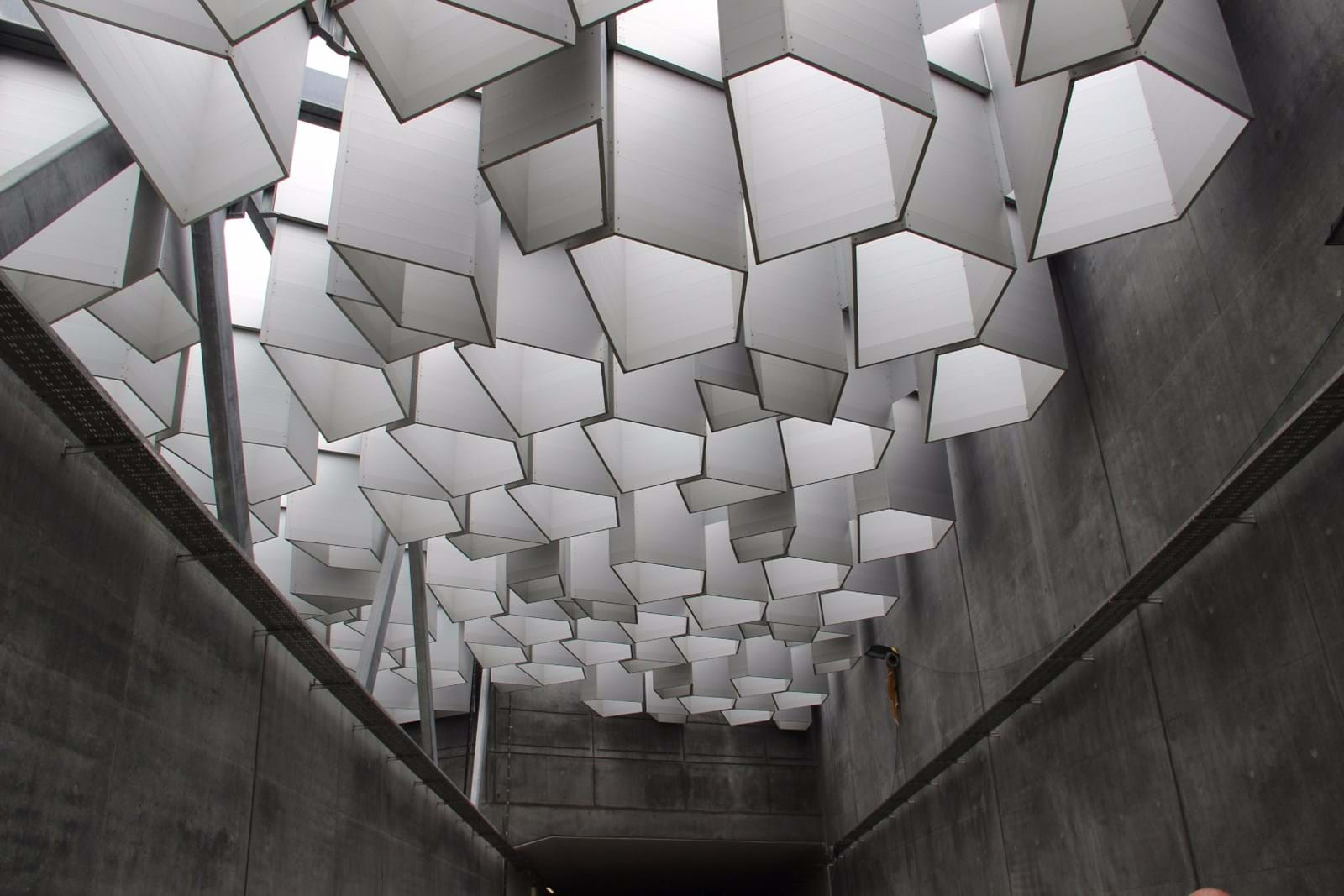
When the company AluSteel from Funen won the contest on manufacture of daylight screens for the Nordhavnsvej project in Copenhagen, Alumeco was the perfect partner for sparring and cooperation. The solution, which gradually reduces the inflow of light in both ends of the tunnel, is a puzzle of daylight screens in processed and assembled aluminium profiles.
- We have had a great partnership with Alumeco for several years, so when we got the Nordhavn project, we obviously had to ask Alumeco to be part of it, says Mads Milling, co-owner of AluSteel.
He continues:
- It is important to us that we maintain the delivery reliability, quality, efficient logistics and other factors, which we know Alumeco for. We have had a great partnership for years. Maybe because we don’t agree on everything from the beginning, resulting in a great dialogue when developing joint solutions.
”Simply perfect... ”
- When we entered the project, the builder wasn’t far in the process. So we sat down with our building project organisers and with Alumeco to find the right profiles for the project. It ended up being a new development of existing profiles, which we subsequently made bigger, says Mads Milling.
- We made a mock-up of the profile, which we brought to a meeting with the Municipality of Copenhagen - the builder of the project. It turned out to be just what they wanted - simply perfect.
Sparring, setup and logistics
For Mads Milling, Alumeco has been an important sparring partner throughout the whole project:
- Alumeco was a great sparring partner during the development phase, since it is a company with huge demands for the employees. This makes them good and skilled people.
- Initially, we should have had the profiles for processing, but I quickly saw the advantage of us receiving the profiles packed after processing at Alumeco. It meant that we got the processed profiles partly assembled directly on site in Copenhagen and it was just a relief that Alumeco was able to handle the whole logistics setup.
12,500 sections semi-manufactured - all processed
- The daylight screens, calculated by the architect, tone and fade the daylight, ensuring a comfortable change between light and ”darkness” when entering and exiting the tunnel. This is a new and interesting way of solving this problem, as both functionality and aesthetics are considered, says Christian Pilgaard, Project Manager at Alumeco and part of the team, working with the solution:
- We needed 15 different aluminium profiles in the shape of building and corner sections, which could be clicked together in different heights and cubic shapes. Together with AluSteel, we further designed a click solution and planned the logistics with partly assembled profiles, so all 12,500 profiles could be assembled as a building kit on site.
Facts about the Nordhavn project:
A whole new district is currently being established in Nordhavn, requiring new access roads, and the tunnels (and daylight screens) are part of this new infrastructure. In this regard, the Municipality of Copenhagen is establishing Nordhavnsvej, connecting the Helsingør motorway with Nordhavn.
When motorists enter and exit the tunnels, they will see that the daylight fades - instead of the traditional sudden change from light to darkness.
Thousands of aluminium profiles, clicked together, result in ”tubes” with different cubic shapes and heights.
The company AluSteel from Funen won the contest on manufacture – and uses Alumeco as sparring partner and supplier.
Alumeco has partnered up with AluSteel throughout the whole process, from development to manufacture of profiles, as well as logistics with direct delivery on site.
The dialogue between the builder (Municipality of Copenhagen), Rambøll and other project parties - concerning external audits, control plans, quality documentation (for surfaces and tolerances) etc. has been close.
The profiles are natural anodised with 25 mu in layer thickness, since the solution is located so close to water. The purpose of natural anodising is that it is decorative and protective. Alumeco has further processed and cut up the profiles, so they are delivered semi-manufactured on site.
Facts in numbers:
20 triangles are used for the daylight screen West
Each triangle is made of a primary steel frame (RHS 450x150x10 mm.)
Each triangle is mounted with a secondary aluminium frame with 12 panels in a hexagon pattern (H: 800 mm x W: 80 mm.)
Different tertiary aluminium frames are mounted in the secondary aluminium, in varying geometrical shapes.
These vary in number between 9-12 units in each triangle and in H: 800 - 2.800 mm x W: 40 mm.
There are a total of 10 different shapes of tertiary aluminium, in 6 different heights:
2 x triangles H: 800 mm.
2 x triangles H: 1.200 mm.
2 x triangles H: 1.600 mm.
2 x triangles H: 2.000 mm.
6 x triangles H: 2.400 mm.
6 x triangles H: 2.800 mm.
Each triangle is about 49 m² big and the daylight screen West is about 980 m² big.
The daylight screen is about 59 m long.
About 70 tonnes of aluminium was used for the West side.
The article was made in cooperation with AluSteel.
/